26.05.2021
Willkommen in der papierlosen Fabrik

In vielen Produktionshallen gibt es noch immer unzählige zeitraubende und fehlerträchtige papiergebundene Abläufe, statt dass anfallende Tätigkeiten und die Dokumentation über digitale und mobile Applikationen zu erledigen. Nicht so bei ZF. Der Technologiekonzern setzt auf einen Industrial-Internet-of-Things-Ansatz (IIoT) mit SAP Manufacturing Integration and Intelligence für eine papierlose Produktionshalle.
In der jetzigen Zeit haben es Automobilzulieferer wie ZF nicht leicht. Einerseits hält die Corona-Pandemie Herausforderungen bereit. Andererseits muss die Transformation von klassischen Produkten zu neuen Angeboten wie E-Mobilität gemeistert werden. „Darüber hinaus spielen die Themen Geschwindigkeit, Flexibilität, Effizienz und Kosten von der Entwicklung bis zur Serienproduktion für uns eine große Rolle. Hier ist Agilität gefragt“, erläutert Reinhold Geiselhart, Senior Manager Smart Factory Engineering bei ZF. Eine besondere Rolle kommen der Automatisierung und neuen Technologien und damit auch der IT zu. So ist sich der Experte sicher, dass Systeme, Tools und Vorgehensweisen integraler Bestandteil des Produkt-Engineerings und der Industrialisierungsprozesse sein müssen. Stabilität und Flexibilität gewinnen an Bedeutung.
Schnelle Verfügbarkeit gefragt
„Um unsere Planungs- und Produktionsprozesse zu beschleunigen, haben wir unter anderem das Projekt ‚papierlose Produktion‘ ins Leben gerufen“, erinnert sich Jürgen Capelli, Teamleiter Smart Factory Initiatives bei ZF. Statt Ordner zu wälzen und mehrere Minuten nach aktuellen Informationen zu suchen oder ineffiziente Papierformulare zeitintensiv zu bearbeiten, setzt das Unternehmen seit neuestem auf eine vollständig digitale Lösung. Eines der Ziele war es, eine digitale Übersicht über durchgeführte Wartungen zu erhalten und somit die Nachvollziehbarkeit zu erleichtern. Etwa drei Aktenordner mussten pro Fertigungsinsel dazu digitalisiert werden.
ZF Group
ZF ist ein weltweit aktiver Technologiekonzern und liefert Systeme für die Mobilität von Pkw, Nutzfahrzeugen und Industrietechnik. In den vier Technologiefeldern Vehicle-Motion-Control, integrierte Sicherheit, automatisiertes Fahren und Elektromobilität bietet ZF umfassende Lösungen für etablierte Fahrzeughersteller sowie für neu entstehende Anbieter von Transport- und Mobilitätsdienstleistungen. Das Unternehmen ist nun mit weltweit 160.000 Mitarbeitenden an rund 260 Standorten in 41 Ländern vertreten.
„Wir haben unheimlich viele Dokumente, die notwendig sind, um ein Produkt herzustellen. Wenn da etwas geändert werden muss, müssen Mitarbeitende die Dokumente vor Ort austauschen – zudem können papiergebundene Dokumente leicht verloren gehen“, sagt Reinhold Geiselhart. Die mögliche Folge: Eine Bearbeitung von Bauteilen auf Basis ungültiger bzw. nicht mehr aktueller Dokumente kann unternehmenskritische Folgen haben. Mit der papierlosen Fabrik will das Unternehmen zudem weg von langsamen Rüstprozessen bei Bauteilwechseln und hin zu einer verbesserten Zusammenarbeit zwischen Anlagenbedienern, Meistern, Qualitätssicherung und Support. Gleichzeitig sollten Medienbrüche vermieden und somit Fehlerquellen eliminiert werden. Und ein zusätzlicher Nebeneffekt: Viele Tonnen Papier sollten eingespart werden.
Arbeitsaufträge digital steuern
Die Anforderungen an die papierlose Fabrik lassen sich also leicht zusammenfassen: Es sollte eine zentrale und erweiterbare Plattform geschaffen werden, um unter anderem die digitale Steuerung von Arbeitsaufträgen zu ermöglichen, bei denen alle relevanten Informationen mit einem Klick in Echtzeit verfügbar sind. „Dabei war uns eine einfache und intuitive Bedienbarkeit mit hinterlegtem Berechtigungsmanagement wichtig. Jeder sollte das sehen, was er tatsächlich benötigt“, sagt Reinhold Geiselhart. Gleichermaßen sollte der Status von Wartungs-, Inspektions- und Reinigungsarbeiten visualisiert werden, für eine höhere Transparenz und Verbindlichkeit. Ebenso standen Bedienerfreundlichkeit für die Anlagenbediener und die Integration der digitalen Lösung in das ERP-System im Fokus.
Arbeitskreis Fertigung
Der Arbeitskreis Fertigung mit seinen über 1.300 Mitgliedern dient dem Erfahrungs- und Informationsaustausch der Anwender von SAP-Lösungen im Wertschöpfungsnetzwerk von produzierenden Unternehmen.
Österreichspezifische Arbeitsgruppe
Die Methode der Wahl, um die papierlose Fabrik zu etablieren, war ein Bottom-up-Ansatz. In einer Art Assessment wurden die Anforderungen der Mitarbeitenden aufgenommen und die wichtigsten Funktionalitäten für die digitalisierte Lösung definiert. Realisiert werden sollte das Ganze zunächst in der SAP HANA Cloud. Doch nach dem Proof-of-Concept wählte ZF Friedrichshafen schließlich SAP Manufacturing Integration and Intelligence (SAP MII) als Datendrehscheibe (siehe Glossar). „Für SAP MII als technische Grundlage haben wir uns vor allem deshalb entschieden, weil unsere Anforderungen auf der HANA-Cloud-Technologie zum Zeitpunkt des Projekts noch nicht so schnell realisierbar gewesen wären. Zudem war SAP MII bereits verfügbar“, ordnet Jürgen Capelli ein. Die Informationen für die Assistant-App der papierlosen Fabrik kommen bei ZF größtenteils aus dem R/3 sowie teilweise aus weiteren Systemen der Produktionsplanung und -steuerung.
Nahtloser Datenaustausch
Das eingesetzte MII-System musste dazu mit dem bestehenden R/3-System so verbunden werden, dass ein Datenaustausch in beide Richtungen nahtlos erfolgen kann und Informationen in Echtzeit zur Verfügung stehen. Die Anbindung zu den SAP-Systemen selbst war technisch nicht so herausfordernd wie anfangs gedacht. Herausfordernder war es für das zehnköpfige Kernteam des Projekts, die hohe Anzahl Stakeholder aus IT, Produktion und Planung zu koordinieren und den für Teile des Projekts angesetzten straffen Zeitplan zu halten. „Außerdem haben wir viel Zeit in die Benutzerfreundlichkeit investiert, um eine möglichst hohe Akzeptanz bei den Mitarbeitenden zu erzielen“, erinnert sich Reinhold Geiselhart. Bis jetzt arbeiten ca. 400 Mitarbeitende in zwei Produktionshallen mit der digitalen Lösung. Ausgerollt werden soll die digitale Produktionshalle jedoch noch in drei weiteren Hallen, sodass mehr als 1.000 Mitarbeitende davon profitieren können. Bestärkt wird das Projektteam bei diesem Vorhaben durch die positive Resonanz der Mitarbeitenden, die die Lösung auf ihren Tablets bereits einsetzen.
Glossar
SAP Manufacturing Integration and Intelligence (SAP MII)
SAP MII soll als Datendrehscheibe die Produktionsebene (Shop-Floor) und MES-Systeme mit dem SAP ERP verbinden und mehr Transparenz in die Produktionsprozesse bringen.
Industrial Internet-of-Things (IIoT)
Unter IIoT versteht man eine Variante des Internet-of-Things (IoT), die im industriellen Bereich angewendet wird. Das industrielle Internet der Dinge kann in vielen Branchen eingesetzt werden, wie z. B. im produzierenden Gewerbe. Einer der wichtigsten Aspekte ist die Verbesserung der betrieblichen Effektivität durch intelligente Systeme und flexiblere Produktionstechniken.
Effizienz gesteigert
„Jetzt ist eine effizientere Arbeitsorganisation möglich. Wir sparen Zeit, die Zusammenarbeit ist besser, und die Teams sind zufrieden“, fasst Jürgen Capelli zusammen. Mitarbeitende in der Produktion haben Anweisungen und Pläne nun direkt digital verfügbar, Verantwortlichkeiten und bereits erledigte Schritte sind klar ersichtlich und können langfristig geplant sowie eindeutig zugewiesen werden. „Wir haben schlichtweg den Verwaltungsaufwand reduziert und dadurch mehr Effizienz erreicht“, lautet das Fazit von Reinhold Geiselhart.
Achtung bei Lizenzmodellen
Einen Tipp für andere, die ebenfalls eine papierlose Produktionshalle etablieren möchten, haben die Experten auch: „Der Schlüssel zum Erfolg ist eine agile und flexible Entwicklung und Implementierung. Es sollte im Vorfeld genau geklärt werden, welche Applikationen und wie viele Lizenzen benötigt werden. Sonst kann es richtig teuer werden.“
In Sachen Lizenzen hatte das Unternehmen eine große Hürde zu meistern, denn die mehr als 1.000 Werker selbst hatten bei ZF keine SAP-Lizenzen, sondern lediglich der Planer. „In der Produktion kann ein Unternehmen einfach nicht die gleichen Lizenzkosten tragen wie z. B. im Engineering-Bereich. Das ist wirtschaftlich nicht machbar. Es handelt sich in der Produktion auch vor allem um Viewer-Lizenzen“, ordnet Reinhold Geiselhart ein. Insgesamt sei hier auf Herstellerseite mehr Flexibilität wünschenswert. „Die ganze Industrie ist noch nicht auf eine umfassende Vernetzung ausgerichtet – das betrifft nicht nur SAP“, ist sich Reinhold Geiselhart sicher.
Wichtige Links
Innerhalb der DSAG werden neue Technologien wie Internet-of-Things unter anderem im Forum Digitale Transformation diskutiert.
Strategisch in die Zukunft
Eine weitere Empfehlung der IT-Experten lautet, in interdisziplinären Teams mit einem agilen Ansatz vorzugehen sowie IT-Strukturen zu schaffen, die nicht nur für einen speziellen Fall geeignet, sondern zukunftsfähig sind. Zukunftsfähigkeit schreibt ZF auch weiterhin groß. So hat das Unternehmen bereits eine digitale Manufacturing-Strategie mit sieben Initiativen erarbeitet, die nun sukzessive vorangetrieben wird. „Dazu gehört, dass wir eine digitale Manufacturing-Plattform entwickeln und uns mit dem Thema Connectivity auseinandersetzen, um eine vernetzte Fabrik zu schaffen“, erläutert Reinhold Geiselhart. Gleichermaßen stehen weitere Themen, wie unter anderem Advanced Analytics, auf der Agenda.
Und was konkret die papierlose Fabrik anbelangt, wäre es auch denkbar, in naher Zukunft weitere Informationen zu digitalisieren, wie z. B. die Schichtplanung oder Trainings für Mitarbeitende. Mit diesen Digitalisierungsbestrebungen möchte ZF nicht nur die Zufriedenheit seiner Mitarbeitenden stärken, sondern auch seine gute Position im Wettbewerb ausbauen.
Bildnachweis: ZF Group + Anna Polywka
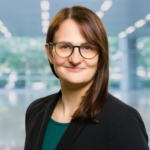
Autorin: Julia Theis
blaupause-Redaktion
blaupause@dsag.de
Schreibe einen Kommentar