Für viele bedeutet das erste Auto vor allem Freiheit. Doch ein Gefährt, das nur von A nach B transportiert, reicht heute nicht mehr. Autonomes Fahren, Elektromobilität und neue digitale Technologien fordern einen Wandel – auch von der Hirschmann Automotive GmbH. Dafür hat der global ansässige Zulieferer mit Stammsitz in Österreich seine Fertigung neu ausgerichtet.
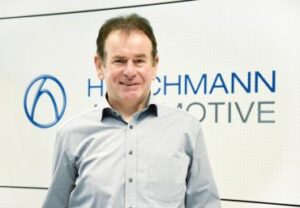
So wie das Auto heute nicht mehr wegzudenken ist, gehört die IT zum Business von Hirschmann Automotive. „Wir müssen technisch stabile, hoch verfügbare Systeme mit Standard-Tools innerhalb kürzester Zeit bereitstellen“, erläutert Wolfgang Klotz, Concepts and Projects Manager bei Hirschmann Automotive. Dazu braucht das Team einen guten Überblick über die Prozesse und muss über Abteilungsgrenzen hinweg integrierte Lösungen konzipieren. „Durch die tiefe Integration im Produktionsumfeld wäre jeder Ausfall der produktionsnahen IT-Systeme schmerzhaft“, so der Experte.
Arbeitskreis Fertigung
Der Arbeitskreis Fertigung mit seinen über 1.200 Mitgliedern dient dem Erfahrungs- und Informationsaustausch der Anwender von SAP-Lösungen im Wertschöpfungsnetzwerk von produzierenden Unternehmen.
Österreichspezifische Arbeitsgruppe:
Neue Fertigungs- und Produktionskonzepte
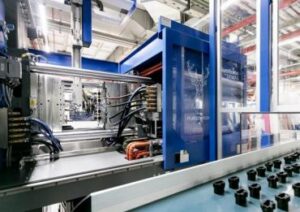
Darüber hinaus müssen Unternehmen und IT stetig steigende Anforderungen an die Rückverfolgbarkeit erfüllen. Je nach Kunde, Projekt und Produkt müssen einzelne Komponenten chargengeführt zurückverfolgt werden. Um das zu ermöglichen, hat Hirschmann Automotive ihre Fertigungs- und Produktionskonzepte grundlegend überarbeitet. So wird die seit Mitte der 1990er-Jahre mit SAP realisierte Linienfertigung abgelöst. „Aus Sicht der Produktion war das Fertigungsdesign strikt darauf ausgelegt, dass Produktionslinien, wie z. B. die Achsverkabelung für einen großen Original-Equipment-Manufacturer (OEM), auch als solche sichtbar waren“, so Wolfgang Klotz. Der Grundgedanke bestand darin, in der Produktion nur wenig von der IT abhängig zu sein. So hätte die Fertigung auch eine Zeit lang weiterlaufen können, wenn das SAP-System ausgefallen wäre. „Mitarbeitende konnten im Produktionslager Material holen, verarbeiten, und bei Fertigstellung wurde das verwendete Material dann retrograd abgebucht“, beschreibt der IT-Experte grob das Vorgehen, das mit der SAP-Serienfertigung umgesetzt wurde.
Ein Nachteil: Dieses Vorgehen lieferte keine detaillierten Informationen.
Mit dem neuen Fertigungskonzept lebt Hirschmann Automotive den Smart-Factory-Gedanken. Nach den Prinzipien von Industrie 4.0 liegt der Fokus nun darauf, die Kundenanforderungen im Bereich der Rückverfolgbarkeit zu erfüllen. „Die Fertigung ist bis ins kleinste Detail geplant und wir gehen in eine Prozesslandschaft über, die tief technisch integriert ist“, erläutert Wolfgang Klotz.
Change-Management erforderlich

Der Fachbereich hat diese Neuerungen nicht nur positiv aufgenommen. Bei vollautomatisierten Prozessen und der tiefen Integration der Maschinen herrscht eine gute Akzeptanz. „Schwieriger gestalten sich Prozesse, bei denen Mitarbeitende manuelle Rückmeldungen geben müssen. Hier entstehen viele neue Arbeitsschritte, und es braucht ein gutes Change-Management“, so der IT-Experte. Die Produktionsmitarbeitenden hatten früher mehr Freiheiten. Sie konnten z. B. entscheiden, welches Werkzeug sie am besten auf welcher Maschine und in welcher Reihenfolge einsetzen. Damit sei man sehr erfolgreich gewesen. Doch hinsichtlich der Rückverfolgbarkeit waren Grenzen gesetzt. So müssen z. B. Prozessparameter aus Maschinen heraus dokumentiert werden, was ein gut integriertes Manufacturing-Execution-System notwendig macht.
Entschieden hat sich das Unternehmen hier u. a. für die Fertigungslösung SAP Manufacturing Execution (SAP ME) und Fertigungsaufträge im ERP ECC 6.0. Hierbei spielte vor allem der Integrationsaspekt eine Rolle. ME soll kombiniert mit SAP Production Planning and Detailed Scheduling (SAP PP/DS; siehe Glossar) eine durchgängige Lösung bieten.
Rückkehr zum Standard
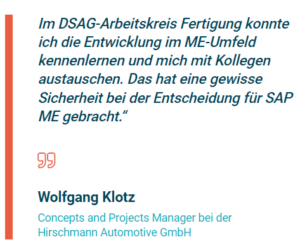
Bisher werden drei Pilotlinien mit dem neuen Ansatz abgewickelt. „Diese Kombination von ME und den Fertigungsaufträgen im ERP-System dient uns als Langzeitarchiv für eine verbesserte Datenerfassung“, sagt der IT-Experte. Das zweite wichtige Entscheidungskriterium für den Umstieg auf Fertigungsaufträge und ME war eine Rückkehr zum Standard. „Wir werden eine umfangreiche Eigenentwicklung für die Übertragung von Produktionseinteilungen aus der Serienfertigung durch ein externes Manufacturing-Execution-System ablösen und so für S/4HANA fit werden“, so Wolfgang Klotz.

Gestartet wurde vor der Einführung von ME mit einer Ist-Analyse der Geschäftsprozesse. Anschließend erfolgten Konzeption und Business-Blueprint sowie die Entscheidung, mit einer überschaubaren Pilotlinie zu beginnen. Zudem kommt die Lösung beim Neubau einer Produktionshalle in Tschechien zum Einsatz. Hier ist ein vollautomatisiertes Kleinteilelager bis hin zur Spritzgussmaschine angebunden. „Das war eine große Herausforderung, denn: Fällt eine Komponente aus, steht die Produktion. Deshalb sind wir stark gefordert und müssen einen IT-Support rund um die Uhr sicherstellen“, beschreibt Wolfgang Klotz. Im Rahmen von Integrationstests wurde geprüft, ob die Produktion mit ME und SAP Manufacturing Integration and Intelligence (SAP MII; siehe Glossar) weiterarbeiten kann, wenn das zentrale System ausfällt. „Alles, was an das ME-System übergeben wurde, wurde abgearbeitet. Das hat uns positiv überrascht“, freut sich der IT-Experte.
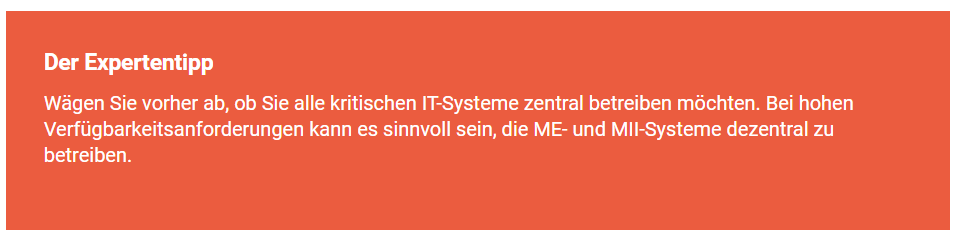
Viele parallele Projekte
Derzeit laufen bei Hirschmann Automotive viele Projekte im Fertigungskontext parallel, was an sich schon herausfordernd ist. „Wir haben einerseits die Umstellung von der SAP-Serienfertigung auf Fertigungsaufträge. Andererseits haben wir ein Projekt, bei dem wir PP/DS als Embedded-Lösung einführen, und wir haben die klassische technische ME-Implementierung“, erläutert Wolfgang Klotz. Gleichzeitig müssen Maschinen integriert und die Mitarbeitenden mitgenommen werden.
Aus technischer Sicht gab es vor allem im Bereich des Spritzgusses bei PP/DS und der klassischen Fertigungsauftragsabwicklung zunächst eine große Hürde zu nehmen. „Wir wollten im PP/DS eine Detailplanung bis hin zum Werkzeug und zur Verfügbarkeitsprüfung abbilden. Es sollte dargestellt werden, welches Werkzeug wir einsetzen wollen, und ob es auch wirklich vorhanden ist“, beschreibt Wolfgang Klotz. Hier musste aufgrund der Vielzahl an möglichen Spritzgusswerkzeugen sowie zahlreichen alternativen Vorgängen und Fertigungsversionen ein hoher Aufwand bei den Stammdaten betrieben werden.

Smart-Factory-Ansatz weiter vorantreiben
Doch all die Arbeit zahlte sich aus. So ist das Unternehmen seinem Wunsch nach einer papierlosen Fertigung nähergekommen. Gleichzeitig freut sich das Team darüber, dass die Rückverfolgbarkeit ermöglicht wird und nun beste Voraussetzungen herrschen, um eine reibungslose Anbindung der Lagertechnik sicherzustellen. Auch künftig will Hirschmann Automotive den Smart-Factory-Ansatz vorantreiben. Was ME anbelangt, so lautet die Devise: „Die Lösung wird dort eingesetzt, wo ein Nutzen erkennbar ist. Das kann z. B. bei der Anbindung von einer Spritzgussmaschine mit automatischen Rückmeldungen sein“, so Wolfgang Klotz. Den Großteil seiner Werke will das Unternehmen mit der Lösung ausstatten.
Bildnachweis: Hirschmann Automotive GmbH, Anna Polywka + Shutterstock
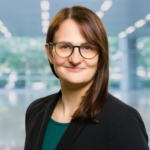
Autorin: Julia Theis
blaupause-Redaktion
blaupause@dsag.de
Schreibe einen Kommentar